Featured Articles
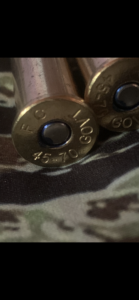
North Woods Big Bore
By Tom Kelley What’s the old saying? “The more things change, the more they stay the same”. Or more accurately, “The more they return to the past.” This is evident in the trend over the last few years back towards lever action rifles. My father was born in 1898. He was a lifelong hunter, like … Continued
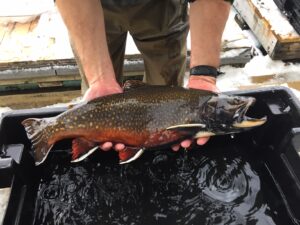
Moosehead Brookie Bonanza
By Suzanne AuClair In recent years, Moosehead Lake has been seeing an ungodly number of these big, fat, native wild brook trout. It has not been the norm. But, it is true. How long this will last, who knows. But for right here, right now, in 2025, anglers are seeing the best of the … Continued
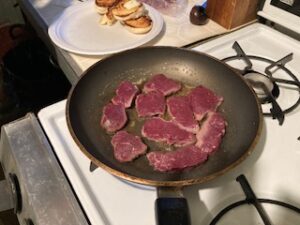
Salt Pork In the Pan
BY V. Paul Reynolds Frankly, I never gave too much thought to the role of salt pork in cooking, outdoors or indoors. I do recall that my mother used it once in awhile when she made fish chowder or baked beans. It had to be part of my vocabulary, though, because I slipped some salt … Continued
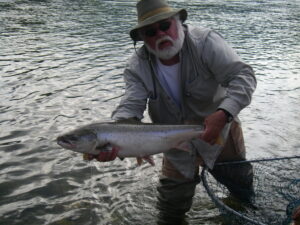
Salmon : Why Aren’t They Big as They Used to Be?
By Randy Spencer If you talk to old-timers who fished the great salmon lakes of Maine—Moosehead, Sebago, East Grand, or West Grand—in the 1950s and ’60s, you’ll hear stories of hefty landlocked salmon tipping the scales at five, six, even eight pounds with regularity. Back then, a 20-inch salmon wasn’t a bragging right; it was … Continued
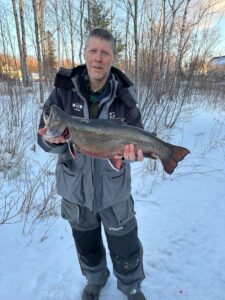
Moosehead New Record Brookie
By V. Paul Reynolds Greenville native and ardent angler Eric Ward is accustomed to hog- wrestling impressive brook trout out of his ice hole and on to the frozen surface of Moosehead Lake. In fact, according to Greenville fisheries biologist Tom Obrey – who keeps an eagle eye on angling successes on the big lake … Continued
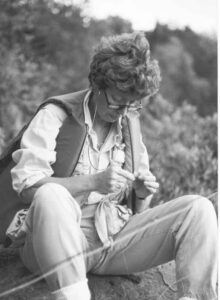
Timely Tips On Tippets
By Bob Mallard While restocking my Fly Vest and Driftboat Bag in preparation for spring last week, I realized just how complex the world of Fly Fishing tippet material had become. As one of the most important components in regard to a properly rigged Fly Fishing outfit, I am surprised that some anglers … Continued
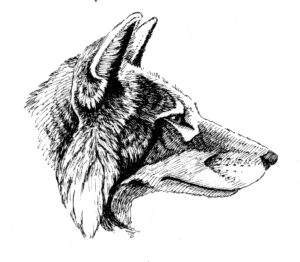
Wolves in a Test Tube
BY Matt Dunlap Sometimes, truth is stranger than fiction. In 1993, the blockbuster science fiction film Jurassic Park had a plotline that a group of paleo-geneticists had extracted dinosaur DNA from fossils, and had been able to create a new generation of velociraptors and other large herbivorous and carnivorous dinosaurs. When, in the movie, everything … Continued
Maine’s Last Indian Scare
Steve Pinkham Maine’s early wars with the various Wabenaki tribes that resided on the Saco, Androscoggin, Kennebec, Penobscot, and St. Croix Rivers, were fought mostly from the mid-1600s to the 1750s, which involved numerous attacks along the coasts of Maine, New Hampshire and along the Merrimac River in Massachusetts. The last attacks on the coast … Continued
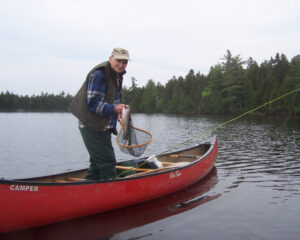
Do Fishermen Lie?
By V. Paul Reynolds As a fisherman myself, as well as a writer who observes other fishermen, I have noticed that we fishermen, in our enthusiasm, do tend to take liberties. There are two common misrepresentations practiced by the angling community. The first is more of an innocent fib, or little white lie. This is … Continued
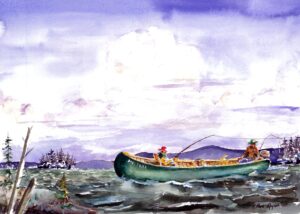
Spring Trolling: Best Waters
By Bud Leavitt Editor’s note: Maine’s late, well-known outdoor writer Bud Leavitt left us his legacy between the pages of his only book, Twelve Months in Maine. In this monthly feature, we reprint selected excerpts from his book courtesy of Bangor Publishing Company. One day at West Grand Lake, Elliot and I were fishing the … Continued